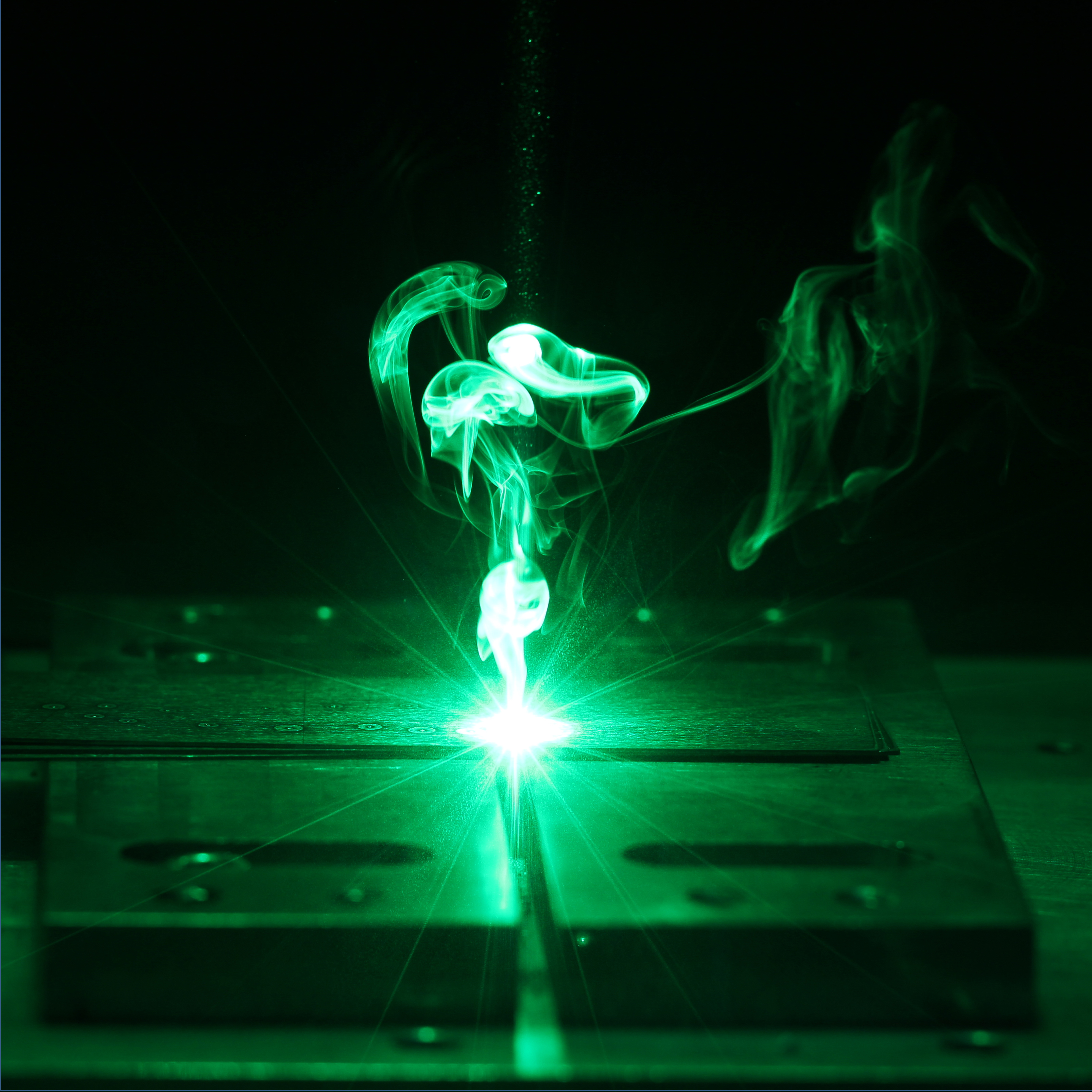
By Ruediger Brockmann
The proceeding limitation of CO2 emissions by government as well as expected shortage of oil resources worldwide associated with increasing cost for fuel results in a global requirement for alternative mobile forms of energy. The development of these alternative forms of energy is summarized within the Mega Trend E-Mobility. Within this Mega Trend the main topics are alternative drives, energy storage systems, concepts for lightweight design and infrastructure for the E-Mobility.
As more than 40 percent of the manufacturing cost of an electric vehicle results from the battery, a significant cost reduction of this key component is required to increase the sales. Therefore many technical developments and political framework have been developed within the last few years. On the political side, all around the world governments support the E-Mobility, e.g., in Germany with a premium of $4,300 for the purchase of a battery electric vehicle (BEV) or plug-in hybrid vehicle (PHEV). The Chinese government supports the installation of charging stations and the purchase of PHEV and BEV with several billion dollars. Although the actual number of electrified cars is very small compared to ICE-cars (internal combustion engine), the number increases very fast every year.
On the technical side, there has been much progress in the performance of the battery and in the production technology. Especially, the big efforts in improving production technology leads to a faster decline in prices for batteries and battery packs than expected a few years ago. The actual price for battery cells is below $215/kWh and is expected to become lower than $108/kWh in the year 2030.
In the context of the developments within these main topics, there are some new technological challenges, for example, cutting of electrode foils, welding of different materials, e.g., aluminum and copper, aluminum and steel, and gastight welding of boxes containing heat-sensitive components. The laser with its high flexibility, its high process speed and its possibility to bring in the energy very selective into the material is very suitable for a high productivity and components of highest quality.
The upper part of Fig. 1 (labeled with “step”) shows the full process chain of battery production. In the lower part beneath the production technology (e.g., “welding”), there are the optics and the laser source suitable for this production step.

Overview of the Process Chain
At the beginning of the production chain the aluminum or copper foil is coated and compressed to manufacture the electrode foil. For anodes you use copper, for cathodes aluminum as carrier material. This foil is produced on a coil which needs to be cut in sheets in a process chain called slitting or sheet cutting. The state-of-the-art technology for this production step is mechanical cutting. A major disadvantage of mechanical foil cutting is the very high mechanical abrasion of the cutting tool. Therefore it is necessary to change the tools frequently, which leads to additional tool costs and fluctuations in cut quality.
Within the next step the taps of the electrode foils need to be welded together. Today, the state-of-the-art technology at this step is laser welding or ultrasonic welding. The technological challenge during this production step is welding thin foils in combination with material mixing, like copper-copper, aluminum-aluminum or aluminum-copper joints. Furthermore, a very low electrical resistance in the fusion zone is required for a high quality battery cell.

The electrode foils are packed in the case during the next production step. This can either be a hard or a soft case, also called pouch-cell or coffee-bag. After packaging, the case is closed and sealed. The welding seam must be gas tight. For this reason, there are high requirements for the welding process. As the electrical parts are already in the case, the thermal energy and power density are limited. Therefore, there are only very few welding technologies which can fulfill these requirements – one of this technologies is laser welding.
In the last step of the cell production, the battery case is filled with electrolyte. After filling, the inlet must be closed, using a welding process with nearly the same requirements as in the previous step.
In the last production step, the cells are combined to battery modules and blocks. Also in this step joining technologies are needed for electrically and mechanically connecting the several cells and modules. As the current delivered by the modules is much higher compared to a single cell, the cross section has to be bigger, but the requirements for the weld seam are the same as for the tap welding.
Welding Copper – Spatter Free
One of the most challenging process steps is the welding of copper without spatters. Especially for welding of the taps made from copper or electric contacts within the electronic parts. To weld this material mostly spatter free, there are two ways – depending on the application. One possibility is the use of a laser with infrared wavelength, high beam quality, and a small spot diameter. The other solution is, to use a laser with green wavelength.

The benefit of the infrared wavelength laser is, that it is a common technology today. But for realizing larger weld width, an oscillation (wobbling) of the laser spot on the workpiece is needed. This means you have to handle an additional process parameter – and this always means a more complex process. By using the green wavelength, additional wobbling can be avoided, as a small focal diameter as a result of the higher absorption of the green wavelength into copper is not needed. Therefore the process is less complex and much more robust compared to the use of the infrared wavelength – especially in the field of battery and electronic parts production with its high production and volume and complex parts a big benefit for the production.

Conclusion
(TruDisk) Lasers are very suitable for welding applications in the field of battery production because they have the ability to machine high-reflecting materials like aluminum or copper. By using an additional scanner focusing optics for remote welding the productivity increases even further. Due to the low total costs of ownership remote welding with (TruDisk) Lasers is an ideal solution for the welding of lithium-ion batteries.

Advantages like a defect-free and hermetic seal weld without holes and cracks and low thermal heat input make laser welding so essential in the manufacturing process of the battery housings.